Injection Mold Flaws & How to Prevent Them
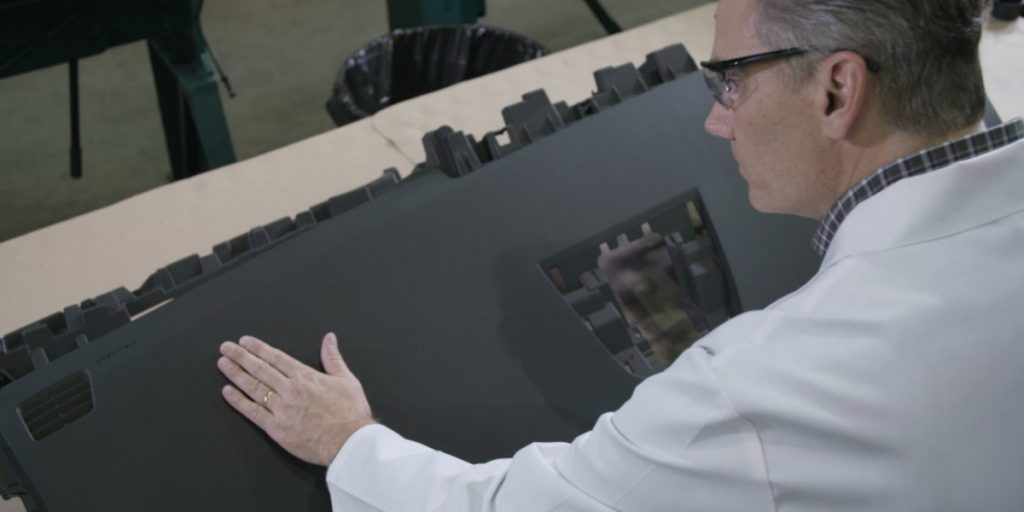
Contamination, Splay, & Delamination
As we said in our last blog post, injection molding practitioners can’t completely avoid all flaws and defects during the process.
However, taking extra precautions to correct any flaws that may occur goes a long way to maintaining the profitability of your business and your integrity in the eyes of your clients.
Today, we’ll look at 3 more injection mold flaws and how you can prevent them: Contamination, splay, and delamination.
Contamination
Simply put, contamination occurs when a foreign substance gets trapped in the molten plastic during the injection molding process. These substances can be anything from extra moisture to dirt, flecks of paint from the interior of your machinery to bugs.
There are usually four sources of contamination: machinery, mold, material, and operator.
Machinery Contamination
If your injection molding machinery is in disrepair or not being correctly operated, oil leaks, dirt, and other matter can get into the plastics.
Some solutions to consider include:
- Repairing any oil leaks as quickly as possible and clean up any grease drips as soon as they happen.
- Always use the hopper lid. Do not improvise by using cardboard boxes or other material.
- Clean the hopper thoroughly between material changeovers. If necessary, wipe the inside of the hopper with a soft cloth dampened with denatured alcohol.
Mold Contamination
A mold that requires moving parts, such as slides, lifters, or other mechanical actions need frequent lubrication to keep them in good working order. However, if too much lubrication is used, excess can find its way into the mold.
Optimizing your use of lubricants is the best way to prevent contamination that can impact the integrity and quality of your plastics.
Material Contamination:
Occasionally, the raw materials used in the injection molding process can become contaminated and negatively impact the finished product.
Sometimes, materials contamination is the result of regrind, or material that has already been through the process once, that has become dirty from the equipment. This contamination can be prevented by keeping equipment more clean, but also carefully checking any regrind that may be used.
Additionally, excess moisture from steam can contaminate the injection molding process. To avoid contamination from water, thoroughly dry all raw material before putting it through the molding process.
Operator Contamination:
Not all injection mold operators are as careful with their processes as they should be. Food and drink that’s kept near the equipment, improper cleaning procedures, or just plain negligence and lack of care can cause expensive flaws to molded products.
Review all cleaning and housekeeping procedures often with your employees, and spot check the floor to be sure the rules are being followed.
Splay
Splay is off-colored streaking in a finished product that’s caused by moisture being trapped in the material during the injection process, or a degradation of the material.
What Causes Splay?
In many cases, splay is caused by excess moisture getting into the molten material as it’s being injected into the mold. This moisture turns into steam in the injection process, leaving the finished product compromised and discolored.
Moisture is best identified as the culprit of your splay if the defect doesn’t occur in the same section of the finished product each time.
Excessive heat also can create an appearance similar to moisture splay. You can identify heat-related splay by checking for signs of stickiness or burning on the finished product, or if there’s an odor of overheated material.
Shear during the injection process also can cause splay, and this type of splay often is repeatable on other molded parts as the issue occurs at the same point in the injection process each time.
How to Prevent Splay
The fix for your splay problem is going to depend greatly upon the cause.
Here are some common fixes for injection molding splay:
- Moisture-related: Ensuring that all material is thoroughly dry before beginning the injection mold process is crucial. Mold leaks also can cause moisture-related splay, so check the mold carefully for any signs of damage or leakage.
- Heat-related: Check that the melting temperature is within the window defined by the materials manufacturer to prevent against overheating. Too much backpressure also can cause the material to overheat and cause splay, so carefully dialing in the amount of back pressure used in the process is important.
- Shear-related: If your piece has smaller gate sizes, you may want to decrease the beginning-of-fill pressure to avoid filling the mold too forcefully. Large changes in temperature from when the material leaves the nozzle and when it enters the mold also can create shear-related splay. Check and properly calibrate both temperatures.
Delamination
Delamination is an injection molding flaw characterized by a flaking surface layer, meaning the layers of your finished piece aren’t adhering the way they should. This is often considered a serious flaw as delamination greatly impacts the integrity and strength of the finished product.
What Causes Delamination?
The most common cause of delamination is contamination of the raw material pellets, either with a foreign material or moisture. When the material is contaminated, the layers are preventing from properly sticking together, causing a separation in the layers.
Additionally, delamination can be caused when two incompatible material types are used in the same piece.
How to Prevent Delamination
Delamination can be prevented in a few ways, including:
- Ensuring that all materials used are compatible with one another.
- Increasing the mold temperature or pre-drying the material if moisture is the cause.
- Ensuring that all materials are properly stored and handled to prevent contamination.
- Consider redesigning the mold to decrease the need for release agents, which can cause contamination and delamination.
Spray Vinyl Coatings for Injection Mold Flaw Repair
Flaws happen. But they don’t have to be costly, nor, do they have to force you to re-run an entire production line thanks to Chem-Pak’s Per-Fix Flaw Repair Coatings. Chem-Pak offers a complete line of spray applied coatings that easily and permanently cover discoloration caused by contamination, splay, flow lines and many other defects in one, fast, easy application. We give molders an efficient tool to correct injection mold flaws, giving you more useable pieces from each run and increasing your business’s profitability. Learn more!