Injection Mold Flaws & How to Prevent Them: Discoloration, Gloss, Jet, & Drag
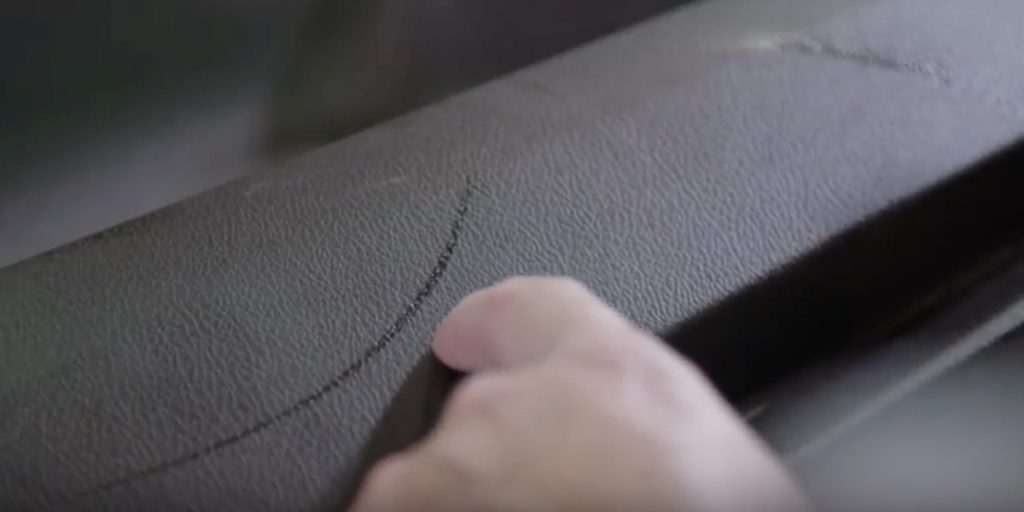
Frequent care and maintenance of all your injection molding equipment, as well as proper employee training, can go a long way to preventing expensive injection molding flaws.
While you can’t completely eliminate flaws from your injection molding business (Wouldn’t that be nice?), you can spend some time tackling problems head-on and trying to find solutions so you’re not using up precious time, money, and materials on flawed products you can’t use.
In this blog post, we’ll look at what the causes and possible remedies for four common injection mold flaws: discoloration, gloss, jet, and drag.
Discoloration
Discoloration occurs any time a plastic product comes out colored differently than you anticipated. This flaw can be widespread, covering large areas of your finished product, or localized to some small areas.
What Causes Discoloration?
There are four common causes for discoloration: problems with your machinery, issues with your molds, injection mold process flaws, and defects with your material.
How to Prevent Discoloration
If your discoloration is the result of machinery problems, begin by thoroughly cleaning your injection molding equipment. This will take care of any leftover materials, powders, or dust that could be causing your contamination, as well as removing any foreign objects that may be blocking the proper working.
Additionally, check that your machines’ temperature gauges are functioning properly, as a temperature that’s too high or too low can cause discoloration.
Issues with the molds could be the result of poor venting, too-small gates, nozzles and sprayers that are too small, or excessive use of lubricants or mold releasers. Clean your machinery and adjust your settings as necessary.
Adjusting these mold settings can help clear up flaws that are the result of an incorrect injection process, such as high pressure, high temperatures, and incorrect injection speeds.
Also check your raw materials for any flaws such as contaminated material, too much moisture, or decomposition of coloring agents or additives. Replacing your materials as necessary should take care of your discoloration.
Gloss
If you are manufacturing a part that is supposed to have a matte or rough finish but it comes out shiny, or vice versa, you’re experiencing gloss.
Gloss can be localized in small areas of your finished product, or widespread, depending on the cause and severity of the flaw.
What Causes Gloss?
Problems with your injection molding process, such as too slow a speed for parts that aren’t supposed to be glossy, or a material temperature that’s too low, are common causes of gloss.
If, for example, your piece has a rough, grooved surface but keeps coming out glossy instead of matte, you could be dealing with a fill speed that’s too slow. The part isn’t allowed to cool as thoroughly before it’s taken out of the mold, leading to a glossier surface.
Additionally, poor material quality or incorrect part design can lead to issues with gloss. If your part isn’t designed to allow for a glossy finish, it’s unlikely that any tweaks will make that finish possible.
How to Prevent Gloss
The way you will approach gloss prevention depends greatly upon the cause of your problem.
If your issue is caused by an incorrect material temperature, an improper injection speed or pressure, or incorrect cavity water temperature, adjusting your machinery until you achieve the desired finish is the easiest direction. This may take some experimenting, so be sure that you’re using all the recommended settings for your chosen raw material.
Gloss problems caused by incorrect part design or improper material mean that you’ll have to rethink some or all of your part’s design. This could be an expensive, lengthy process, but it will pay off in the long run once you’ve got all the factors dialed in properly.
Jet
Jetting shows up as wavy folds on the surface of your finished piece and can, depending on location and severity, severely impact the safety of your finished part.
What Causes Jetting?
When molten plastic fails to stick to the surface of your mold due to the injection speed, it flows into a different area of your finished part and solidifies as wavy folds.
Jetting mostly occurs when your melt temperature is too low, making your melted plastic too viscous. This increases the resistance as the molten plastic flows through the mold, making it more difficult to stick to your mold.
When this too-cool material comes into contact with the surface of the mold, it rapidly cools down and hardens where it shouldn’t.
How to Prevent Jetting
There are three things you can do to help decrease the occurrence of jetting:
- Increase the temperatures of your mold and melt
- Increase your gate size so you get a slower injection speed
- Optimize gate design for adequate contact between the molten plastic and the mold
Drag
If your plastic parts come out of the mold with surface scratches, you may be experiencing drag.
What Causes Drag?
Drag is usually caused by an improperly designed ejection system, or one that is misaligned.
How to Prevent Drag
When designing your part molds, you need to keep in mind the correct angles necessary to easily eject your finished parts. If you’ve got a fairly smooth part that’s parallel to your mold design, ½ degree to 2 degrees is usually sufficient to prevent drag marks. For parts that are more highly grooved, you may need to adjust your mold to suit angles up to 5 degrees.
Checking these angles and either realigning your ejection system for easier release or redesigning it to support proper ejection should prevent those scratches.
High-Quality Spray Coatings for Injection Mold Flaws
Keep your business on track – and on budget – with high-quality spray coatings to fix injection mold flaws from Chem-Pak. Chem-Pak offers a full line of spray-applied coatings to quickly and completely cover discoloration caused by contamination, flow lines, splay, and a variety of other defects. Learn more today!