Injection Mold Flaws & How to Prevent Them: Flow Lines, Knit Lines, & Blush
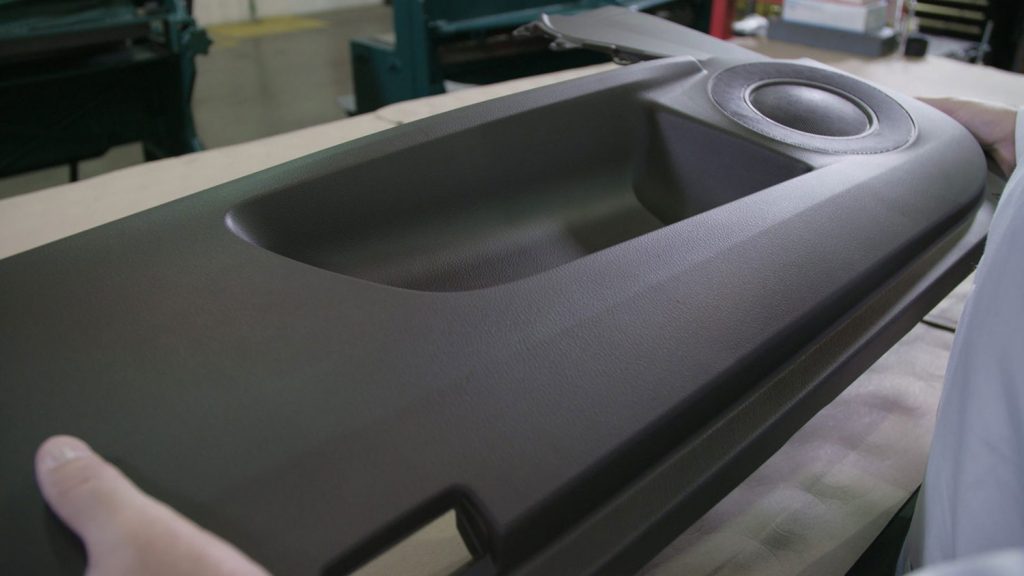
Preventing Flow Lines, Knit Lines, & Blush
Injection molding isn’t an exact science, and there is a lot that can go wrong in getting your plastic pieces ready for market.
While frustrating and sometimes costly, injection molding flaws can’t be fully avoided. However, you can make small changes to your injection equipment and processes to help you decrease the number of flaws that result from the injection molding process.
Here are 3 common injection molding flaws and how to prevent them from happening in the future:
Flow Lines
Flow lines appear as a wavy pattern on the surface of your plastic parts. They usually are a slightly different color than the rest of the piece, and typically occur on more narrow sections of the molded item.
They also can appear as ring-shaped patterns near the entry points of the mold.
Most flow lines don’t impact the functionality or integrity of the molded item, but they can be unsightly and impact your ability to resell the piece to a client.
What Causes Flow Lines?
Flow lines are often the result of variations in the cooling speed of the plastic as it flows in different directions through the mold. They also can occur when you’re creating pieces of differing thicknesses, as the thinner areas cool before thicker areas are fully filled, causing flow lines.
Molten plastic cools very quickly, and flow lines often occur as more hot plastic flows past parts that have already become cool and gummy.
How to Prevent Flow Lines
There are a few adjustments that you can make to your injection molding process to prevent flow lines, including:
- Increase the injection speed, pressure, or material temperature: Slow-moving molten plastic is more likely to cool quickly and cause flow lines. Increasing one of the variables on the material you’re using helps the product move more quickly, fully filling the mold before it begins to cool.
- Round the corners of the mold where wall thickness increases: This helps keep flow rate consistent to the thicker sections and prevents flow lines.
- Relocate mold gates farther from the mold coolant: Providing further separation between the injection point and the cooling apparatus will increase cooling time and decrease flow lines.
- Increase nozzle diameter: This increases flow speed and prevents early cooling.
Knit Lines
A knit line is the spot where two flows meet. When these areas are visible, it can pose no problem at all to the piece, be nothing more than a cosmetic flaw, or can be a source of major structural problems for your piece.
Knit lines often occur when two flows meet and are held at different temperatures, leaving a line between.
How to Prevent Knit Lines
If you’re creating large pieces, knit lines can cost you a great deal of money in lost parts. Here are a few ways to prevent knit lines in your plastic parts:
- Increase material temperature: Higher temperatures on both materials prevent one section from cooling too quickly.
- Increase injection speed and pressure: Faster-moving materials will meet more quickly so one doesn’t cool too soon.
- Redesign the mold: Redesigning the mold to eliminate partitions between sections will remove knit lines altogether.
- Switch materials: Materials with lower melting temperatures or viscosity allows for faster flow and slower cooling.
Blush
Blush is a cloudy discoloration usually found around an injection gate. However, blushing can be found throughout the surface of a molded plastic piece.
A molded piece with blushing is often very structurally weak due to the loose molecular structure.
This can be caused by an improperly sized gate hole, a high injection speed, low injection pressure, improper melt temperature, too-small nozzle diameter, or incorrectly located gates.
How to Prevent Blushing
If you can find the cause of your injection molding blushing, you can adjust your equipment or process to prevent it, including:
- Fix gate hole sizing: A gate hole that is too small or the wrong size for the material will cause blushing, Check your gate’s hole size against the type of material you use and the relative thickness of your finished product and see if that fixes the problem.
- Decrease injection speed: If the mold is filled too quickly by a high injection speed, it can have a negative impact on the material at the gate hole. Adjusting the injection speed so your mold fills more slowly allows the material to fill the space with less pooling.
- Adjust melt temperature: Check the temperature of your material against the specifications to see if that takes care of the issue.
- Increase nozzle diameter: If your injection nozzle is too narrow, the material doesn’t flow out at a fast enough rate, causing pooling. Widening your nozzle diameter allows material to flow freely and properly fill your mold.
- Relocate gate holes: If your gates are positioned closer to more narrow sections of your piece, they will begin to harden first and cause less material to flow to the thicker areas. Moving your gates to areas with more thickness should alleviate this issue.
Plastics Coatings for Injection Molding Flaw Repairs
No matter how careful you are and how much you adjust your equipment and processes, some injection molding flaws are unavoidable. Save time, money, and frustration using high-quality plastics coatings from Chem-Pak. You get more useable pieces, increasing profitability for your business. Learn more!